This review paper explores the rationale behind the advancement of materials designed to serve as radiation shields and thermal barriers in space missions and high-altitude flights. It highlights the significance of ongoing research and the critical need for improvements to ensure effective protection against harmful radiation and extreme thermal environments.
The development of thermal protection systems and temperature-regulating materials for spacecraft is crucial due to the harsh conditions encountered in space. Astronauts, particularly those on missions beyond low Earth orbit, are exposed to intense high-energy radiation, which poses serious health risks. Key concerns include the potential for cancer development, Acute Radiation Syndromes, and damage to multiple physiological systems. Therefore, a comprehensive understanding of these risks is vital to devise appropriate and effective prevention strategies.
Solar Particle Events (SPEs): Solar flares and coronal mass ejections (CMEs) can release sudden bursts of high-energy protons and heavy ions, posing a significant radiation hazard to both spacecraft systems and human occupants. Effective radiation shielding is therefore essential to mitigate the risk of acute radiation sickness and other adverse health effects in astronauts.
These events are particularly hazardous, as they can also disrupt or damage onboard electronics and sensors, potentially causing malfunctions or the failure of critical mission components.
The materials examined in this study include polyethylene, Kevlar, ablative compounds, and advanced composites—each commonly used in spacecraft construction for their protective roles. Among the key findings, it is evident that both polyethylene and Kevlar provide comparable effectiveness in reducing radiation dose rates within space environments. During atmospheric re-entry, ablative materials are employed for thermal protection, while multi-layer insulation systems play a crucial role in managing spacecraft thermal control.
This underscores the importance of understanding material properties and their performance under extreme space conditions, which is essential for ensuring astronaut safety and the overall success of missions. As space exploration extends toward longer-duration missions and increasingly hostile environments, the development of novel materials for enhanced radiation shielding and efficient thermal regulation will be central to achieving sustainable exploration and advancing scientific research beyond Earth’s boundaries.
The foundation of theory (theoretical framework)
In the fields of space engineering, aerospace aviation, and high-altitude flight, radiation and thermal protection represent some of the most critical initial challenges. Space is an inherently extreme and unpredictable environment, exposing both humans and electronic systems to significant threats from cosmic rays and solar radiation, including solar flares.
Cosmic rays—high-energy subatomic particles originating from beyond the solar system—possess the ability to penetrate spacecraft structures, potentially damaging biological tissues and sensitive onboard electronics. Similarly, solar flares can drastically increase radiation levels, further emphasizing the necessity for robust and effective shielding solutions to ensure both crew safety and mission reliability.
In addition to radiation hazards, spacecraft and high-altitude aircraft must contend with extreme temperature variations. In space, for instance, spacecraft can become intensely hot when their solar panels absorb direct sunlight, yet experience dramatic temperature drops in the shadowed regions of celestial bodies where solar energy is absent. These conditions can expose spacecraft to temperatures exceeding 200 °C in sunlight and dropping below –250 °C in darkness. Similarly, high-altitude aircraft face significant thermal challenges due to reduced atmospheric pressure and rapid temperature fluctuations at high elevations.
The development of effective thermal protection systems, therefore, becomes a critical design consideration—often among the final but most complex barriers to mission readiness. These protective materials must not only provide high thermal resistance but also remain lightweight to meet the stringent payload and performance requirements of aerospace applications.
Radiation and thermal challenges
Radiation in space primarily consists of Galactic Cosmic Rays (GCRs), Solar Particle Events (SPEs), and ultraviolet (UV) radiation, particularly at higher altitudes. Each of these radiation types presents distinct characteristics and implications for both human health and technological systems in space. Understanding their nature, intensity, and effects is essential for ensuring the safety of astronauts and the reliability of space equipment. As space missions venture farther and longer, comprehensive knowledge of these radiation forms becomes increasingly vital for the design of effective shielding strategies and mission planning.
Galactic Cosmic Rays (GCRs) GCRs also referred to as cosmic rays are energetic particles which are from outside the solar system and consist mostly of hydrogen protons and other heavier atomic nuclei.
They are dangerous to the health of the astronauts because they can easily penetrate space craft and human tissue causing possible carcinogenic consequences GCR is even more exposed in deep space since the earth magnetic field does not afford much cover ` Solar Particle Events (SPEs)
SPEs are high energy particles radiations from the sun especially during a solar flares and CME’s
Solar Particle Events (SPEs) are typically episodic in nature, capable of producing sudden and intense bursts of radiation. In contrast, Galactic Cosmic Rays (GCRs) represent a continuous, low-level background radiation that persists throughout space. While both pose significant risks, SPEs can escalate rapidly, especially during solar storms, necessitating timely and adaptive protective measures for astronaut safety.
The Effects of High-Altitude Ultraviolet Radiation:
An increase in altitude corresponds with heightened exposure to ultraviolet (UV) radiation, as the thinner atmosphere at higher elevations absorbs less solar radiation. This elevated UV exposure poses significant health risks, including skin damage and an increased likelihood of cancer for astronauts and high-altitude aviators.
To mitigate these risks, appropriate protective measures must be implemented, such as the use of specially designed space suits and radiation shielding. These systems are essential to ensure the safety and well-being of personnel during space missions and extended high-altitude operations.
How do extreme temperatures in space affect spacecraft materials?
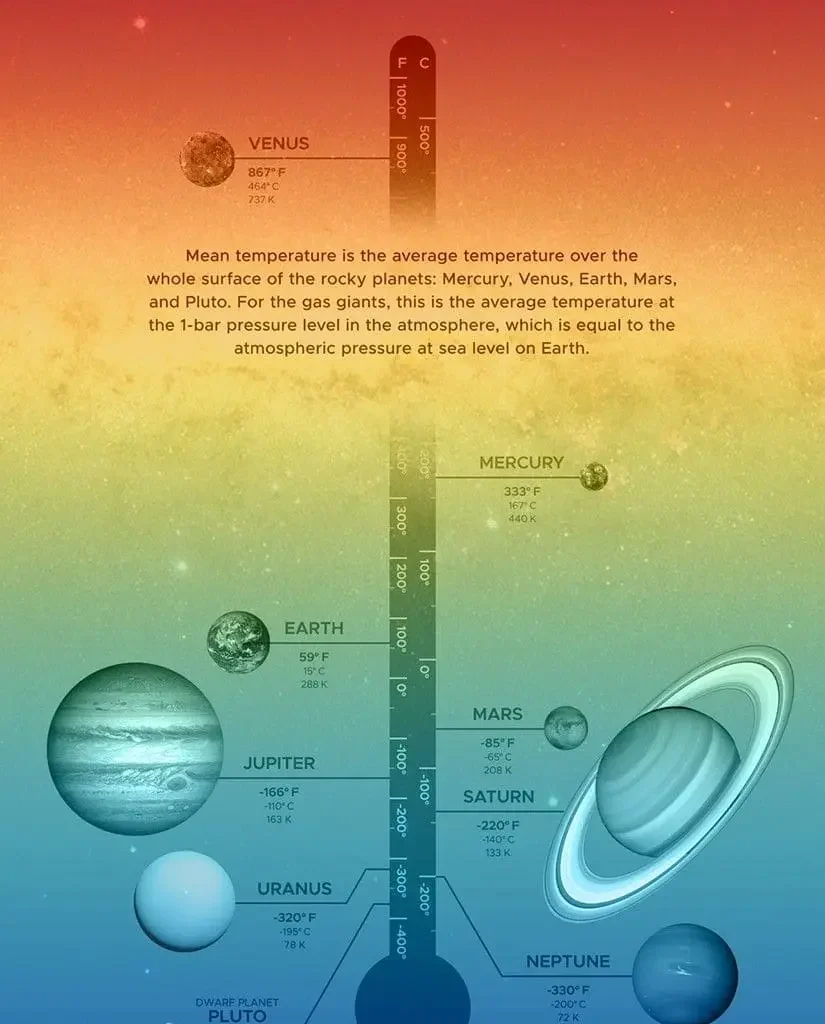
The space environment exerts a significant influence on spacecraft systems, primarily through extreme temperature variations. These temperature fluctuations can directly affect the structural form and functional reliability of spacecraft materials. Combined with intense thermal, mechanical, and chemical stressors, such conditions may lead to mechanical failures, degradation of material integrity, loss of critical properties, and even corrosion over time.
To ensure mission durability and safety, advanced material solutions are required that can withstand these hostile conditions. Below are several ways in which extreme temperature environments impact spacecraft components:
Material Degradation
- Corrosion: Metals used in spacecraft construction are vulnerable to degradation under fluctuating temperatures and intense radiation, leading to structural failures and potential leakage issues [9].
- Thermal Stability: High-temperature polymers used in thermal protection systems must maintain their structural integrity to perform effectively during high-stress phases such as atmospheric reentry and hypersonic flight .
Mechanical Properties
- Dynamic Response: The mechanical properties of materials, such as yield strength, can degrade under high thermal loads. For example, the yield strength of alloys like Hastelloy X significantly decreases at temperatures at or above 900 °C, affecting their load-bearing capacity .
- Deformation Behavior: Elevated temperatures can lead to increased out-of-plane deflections and altered deformation modes, which may reduce structural performance under dynamic or shock loads.
Testing and Development
Further testing under simulated space conditions is crucial to evaluate how candidate materials respond to long-duration exposure. This includes thermal cycling, vacuum environments, and combined radiation-thermal stressors, allowing engineers to develop reliable protective systems for current and future space missions.
Effective materials for radiation and thermal protection
Effective materials for radiation and thermal protection exhibit distinct properties that enhance their performance under extreme temperature and radiation conditions. Key attributes such as density, chemical composition, and structural configuration play a crucial role in determining a material’s ability to attenuate radiation and regulate thermal loads. These factors directly influence the shielding efficiency and heat management capabilities of the material.
The following sections will examine these material properties in greater detail, along with their implications for spacecraft design and safety. In particular, the radiation shielding property serves as a critical parameter for evaluating and selecting materials suitable for aerospace applications. This parameter allows for the pre-qualification of materials before deployment, ensuring their effectiveness in real-world mission environments.
Material density and elemental composition significantly influence a material’s ability to attenuate radiation. High-density polymers such as High-Density Polyethylene (HDPE), when combined with additives like Aluminum Hydroxide [Al(OH)₃] and lead-based compounds (e.g., Pb₂₃), exhibit enhanced gamma-ray attenuation capabilities. Additionally, exposure to certain radiation levels has been shown to increase the tensile strength of these materials, contributing to their mechanical robustness in space applications.
Polymer Composites
Innovative radiation shielding has also been achieved through the development of lead-free polymer composites. For instance, the incorporation of silicon and boron carbide into ethylene-vinyl acetate (EVA) matrices has resulted in materials with significant shielding efficiency. These composites have demonstrated acute X-ray attenuation of up to 91% at 80 keV, making them strong candidates for lightweight, non-toxic radiation protection in aerospace and medical environments .
Heavy Minerals
Composite materials formulated with heavy mineral fillers such as Ilmenite and Zirconium exhibit reduced radiation transmission, particularly at specific photon energy levels. These materials are effective in radiation shielding due to their high atomic numbers, which enhance photon attenuation through increased interaction probabilities, making them suitable for use in radiation-sensitive environments .
Thermal Management
- Thermal Stability: Certain composites, notably those based on High-Density Polyethylene (HDPE), have demonstrated enhanced thermal stability. This characteristic is essential for applications involving sustained exposure to high temperatures, such as in spacecraft reentry or propulsion systems .
- Neutron Absorption: Incorporating Ultra-High-Molecular-Weight Polyethylene (UHMWPE) with boron carbide (B₄C) results in composites capable of slowing and absorbing neutrons, providing both radiation shielding and thermal control. This dual functionality is particularly advantageous in environments with mixed radiation fields, such as space or nuclear reactor shielding .
Differences in Requirements: Radiation vs. Thermal Protection
Radiation and thermal protection systems are designed with fundamentally different material requirements due to the distinct nature of the challenges they address. Radiation shielding primarily depends on a material’s density and atomic number, which enhance its ability to attenuate or absorb ionizing radiation such as gamma rays, X-rays, and neutrons. In contrast, thermal protection focuses on a material’s thermal conductivity, heat capacity, and stability under extreme temperatures, ensuring resistance to both high heat (e.g., during atmospheric reentry) and cryogenic conditions.
For example, heavy minerals like Ilmenite and Zirconium are highly effective for radiation shielding due to their high atomic mass but may exhibit poor thermal insulation properties [15][16]. This contrast highlights that materials suitable for one type of protection may not perform well under the demands of the other.
Therefore, it is critical to recognize that radiation protection and thermal protection, though equally essential, require distinct strategies and material characteristics. A one-size-fits-all approach is insufficient; instead, tailored solutions must be developed for each domain to ensure optimal performance and safety in the severe conditions of space environments.
Key Lessons from Material Testing in Space
1. Adaptation to Harsh Space Environments
Materials must withstand extreme conditions such as:
- Radiation exposure
- Severe temperature fluctuations
- Micrometeoroid impacts
Research aboard platforms like the ISS (International Space Station) shows that different materials react uniquely under these conditions, making such testing invaluable.
2. Focus on Safety and Reliability
Selection of materials should factor in:
- Worst-case mechanical performance
- Resistance to environmental factors
Previous mission failures highlight the consequences of poor material choices, emphasizing the need for integrated safety evaluations.
3. Documentation and Knowledge Sharing
- Thorough documentation is essential in all phases of material testing and project execution.
- NASA’s strategy of documenting failures prevents repetition of mistakes and supports effective communication between teams.
4. Strong Management and Engineering Practices
Early mission setbacks often stemmed from:
- Weak program management
- Lack of strict engineering discipline
- Ensuring quality and reliability through structured procedures is key to avoiding future mishaps.
Ensuring quality and reliability through structured procedures is key to avoiding future mishaps.
5. Embracing Evolution and Innovation
- While past lessons provide a strong foundation, new technologies and mission goals may introduce unforeseen risks.
- Space programs must encourage continuous learning, adaptability, and creative problem-solving.
Empirical research
Methodologies in Empirical Research
A variety of testing methods and simulations constitutes empirical research methodologies for
material evaluation in aerospace applications. Each of these methodologies includes ground
based tests, flight tests and in situ data collection, which serve specific purposes in material
evaluation.
Ground-Based Testing
Thermal Vacuum Chambers: These replicate space conditions to assess the performance of
our materials in really extreme temperature and vacuum. These tests are improved with
innovations in controlling radiation flux.
Radiation Labs: By means of accelerator tests, radiation shielding properties of materials such
as Kevlar and Nextel have been evaluated to determine their efficacy against the cosmic
radiation that is necessary for human safety in space .
Flight Tests
Flight tests are a source of real world data about material performance in the space
environment. But these tests are critical to validating ground based results and to run as
reliably as possible during missions.
In-Situ Space Data Collection
Data collected from materials in actual space conditions gives us an opportunity to evaluate
long term performance and degradation information that ground tests do not capture so well.
Of course ground based tests and simulations are necessary for initial evaluation, however,
the unique environments of the space can not be predicted and can not be guaranteeing
material integrity over time. The use of this dual approach make the materials used in
aerospace applications with higher reliability.
Radiation Protection Materials
Recent work on radiation protection materials has indicated several effective composites,
particularly polyethylene and boron composites. With various materials screened out, these
studies indicate which materials have the potential to shield different types of radiation, such
as neutrons and gamma rays. This summary encourages the reader to read further about key
findings from empirical studies on these materials in the following sections.
Polyethylene-Based Composites
Radiation shielding high-density polyethylene (HDPE) composites reinforced with boron carbide (B4C) and different fillers have shown to be highly effective. Composites of 10% and 30% B4C and iron oxide have shown better shielding of both fast neutrons and gamma rays compared to pure HDPE[24].
Boron and Hydrogen Hybrid Materials
Hydrogen rich aromatic polymer containing boron has been efficacious against high energy
radiation. It turns out boron containing polysulfone functions better to shield neutrons and
alpha particles than other polymers, and polyetherimide records good results with shielding
protons.
Boron Nitride Nanotubes, also known as BNNT
The neutron shielding of boron nitride composites, in particular combined with HDPE, has
been shown to be excellent. These composites were shown, through Monte Carlo simulations,
to be capable of significantly reducing effective radiation exposure compared with traditional
materials, such as aluminum [26].
However, although these materials demonstrate promise, application of these materials in
radiation protection contexts is hindered by manufacturing complexities and related cost effectiveness.
Thermal Protection Systems (TPS)
Thermal Protection Systems (TPS) are highly critical for aerospace applications in such high
temperature environment. Recent empirical work has shifted attention to ablative materials
such as PICA and AVCOAT, ceramic composites, and Multi-Layer Insulation (MLI). We
present this synthesis that highlights the performance and advances in these areas.
Ablative Materials
PICA and AVCOAT: It was shown in [27], that the AVCOAT like systems have a well defined
degradation behavior under high heating rates, and a kinetic analysis also shows an overall
error of 1.5% for modeling mass loss. Thermal protection PICA, with its lightweight and high
temperature resilience, has been key for missions demanding such resilience.
New Developments: The QCF/SPA composite also exhibits outstanding ablation resistance
and thermal insulation properties [28]: it has a mass ablation rate of 0.014 g/s under extreme
conditions.
Ceramic Composites
High-Temperature Resilience: As an indirect result of research, ceramic composites are being
fabricated and tested and found to have greater thermomechanical strength and stability as
compared to plastic at temperatures exceeding 2500 °C, ideal for use in reentry vehicles [28]
Multi Layer Insulation (MLI) Systems
Thermal Efficiency: System designed for MLI have properties such as those specifically
designed to minimize heat transferred, which is needed to maintain spacecraft integrity under
extreme thermal conditions. Advanced materials and design strategies [29] make these
systems more effective.
However, the benefits of these TPS materials are highly promising, despite future challenges
optimizing these systems to meet the requirements of future missions (particularly to Mars),
where the very extreme thermal environment will push the boundaries of current technology
Findings from Space Missions and High-Altitude Tests
Critical lessons to the performance of materials under extreme conditions come from space
missions and high altitude tests. Spacecraft environments have been investigated in a number
of studies as to how different materials are affected by radiation, atomic oxygen and other
thermal cycles. These findings are very important for making certain that materials used in
space applications will prove reliable and long lived.
Material Degradation in Space Environments
Radiation Effects: Optical and mechanical properties of materials subject to high energy
electrons and atomic oxygen in low Earth orbit (LEO) have to be well characterized before
and after exposure.
High-Performance Fibers : Mass loss and changes in tensile strength were found in testing of
fibers like Kevlar and Vectran with atomic oxygen erosion and UV radiation.
Ground Testing & Simulations Outgassing and Impact Resistance: The studies into carbon based materials emphasized the importance of outgassing properties and withstand hypervelocity impacts [32] required for spacecraft functionality.
Mars Suit Materials: Larson (2017) showed that mass loss was slight, but tensile strength was
significantly reduced and therefore selection of material for future missions was affected.[33]
Research gap
Current Limitations in Material Performance
Aerospace Materials: Performance Limitations
- Mechanical and chemical properties under extreme conditions were insufficient.
- The overall weight of the aircraft is a challenge to performance.
- Problems of fretting wear and stress corrosion cracking.
- Materials at high temperatures; incapability.
- Oxidation resistance that limits material integrity.
Existing Materials as Flaws in the Radiation Shielding and Thermal Management
- They may not protect against radiation well enough to protect space vehicles and payloads
in the course of a mission.
Due to the potential of failures during atmospheric entry, many materials do not have the proper properties to survive extreme thermal conditions. Therefore, the variability in manufacturing processes can lead to material property inconsistencies causing thermal management or radiation shielding capability problems.
These shortcomings illustrate the need for the development of better materials that are
tailored, specifically for application to mission requirements.[34]
Can You Balance Material Weight, Strength, and Effectiveness?
- Weight vs. Strength : The first challenge in achieving a lightweight design while having sufficient strength is. Promising high performance fibers such as Vectran and Spectra are plagued with problems such as stress concentration, fatigue .
- Material Flexibility : At low temperature, materials must be flexible, which can affect strength. However, silicone rubber is flexible, and has high gas permeability and low toughness.
- Seam Design: Cinderella construction: structurally efficient joints that are strong as the base material is critical. Joint strength and material effectiveness are substantially dependent on adhesive and seaming technology choice.
- Environmental Resistance: Materials must be able to withstand harsh conditions such as UV exposure and extreme temperatures, which can degrade them and shorten their lifespan.
The technology of making materials that are small enough needs continued research and
development to strike a balance between the competing requirements.
Gaps in Testing and Simulation
- Bounding Aeroheating Parameters: Certifying thermal protection systems (TPS) becomes challenging when the thermal environments cannot be fully defined, or when multiple aeroheating parameters cannot be replicated simultaneously.
- Higher Uncertainties: Under extreme conditions, ground testing environments exhibit greater uncertainties, especially in terms of facility calibration and the reliability of analytical predictions.
- Atmospheric Composition: Replicating planetary atmospheric compositions—such as hydrogen/helium (H₂/He) mixtures for gas and ice giants—poses significant challenges during testing.
- Sample Size Limitations: Restrictions on test sample sizes for qualifying seam designs can reduce the reliability of the results.
- Lack of Computational Tools: There is a shortage of computational tools capable of accurately simulating critical TPS performance features, such as failure initiation and propagation.
The Effect of a Lack of Long Term Testing Data on Material Reliability
- Inadequate Verification: In the absence of long-term testing data, validating the robustness of thermal protection systems (TPS) against failure under extreme conditions is challenging.
- Unpredictable Thermal Response: Limited available data makes it difficult to accurately predict a material’s thermal behavior, which hinders the ability to guarantee mission success.
- Increased Uncertainties: Elevated uncertainties in ground testing environments—especially due to the absence of long-term data—undermine the reliability of analytical predictions.
- Re-qualification Needs: As heritage raw materials like carbon phenolic become increasingly scarce, the need for re-qualification of alternative materials is growing—made more complex by the lack of sufficient long-term performance data.
Challenges in Challenges in Simulating Space and High-Altitude Conditions
- Extreme Heating Environments: Simulating the extreme entry conditions encountered at planets like Venus, Saturn, and the Ice Giants is particularly challenging, with heat fluxes exceeding 2000 W/cm² and pressures above 2 atmospheres.
- Simultaneous Parameter Achievement: Certification is complicated by the inability of laboratory environments to simultaneously replicate multiple aeroheating parameters—such as heat flux, pressure, shear, and enthalpy—required for accurate thermal protection system validation.
- Atmospheric Composition: Test flows that closely replicate the atmospheric compositions of gas and ice giants—such as hydrogen-helium (H₂/He) mixtures—have yet to be accurately achieved in experimental settings.
- Test Sample Size: Limitations in the size of test samples used to qualify seam designs can hinder the accuracy and reliability of simulation results.
Emerging Needs for Future Missions
Radiation and Thermal Protection Material Requirements for Future Missions
- Enhanced Radiation Resistance: As future missions will involve long term missions, with
humans exposed to high levels of radiation, these materials will be needed. - Improved Thermal Management: Spacecraft must operate reliably in extreme thermal environments—particularly during re-entry and high-altitude conditions—requiring materials that can effectively withstand and regulate such conditions to ensure safety and performance.
- Durability Under Harsh Conditions: In extreme space environments—characterized by temperature fluctuations and vacuum—materials must maintain their structural integrity and performance over extended periods.
- Integration of Advanced Technologies: Future interplanetary missions will require the integration of advanced technologies—such as active thermal control systems and radiation sensors—into thermal protection materials.
Addressing Research Gaps for Deep Space Missions
- Conclusion: Further research is needed to understand the effects of space radiation on biological systems—particularly T lymphocytes—in order to better protect astronauts during long-duration missions.
- Development of Advanced Materials: To ensure astronaut safety and mission success, research should focus on developing new radiation and thermal protection materials capable of withstanding the extreme conditions of deep space.
- Integration of Technology: Enhancing operational procedures and mission safety can be achieved through the integration of technologies such as Automatic Dependent Surveillance–Broadcast (ADS-B) and advanced thermal management systems in experimental payloads.
- Collaboration Across Disciplines: Partnerships between universities and space agencies can foster multidisciplinary collaboration, helping to address current challenges in space exploration.
Advancements are needed in material science to ensure the safety of manned and unmanned
missions:
- Radiation-Resistant Materials: Developing materials that offer effective shielding against various types of space radiation—and remain stable under extreme temperatures and environmental conditions—is essential for ensuring astronaut safety during long-duration missions.
- Thermal Protection Innovations: The development of advanced thermal protection systems is crucial for withstanding the extreme temperature variations encountered during spacecraft re-entry.
- Durability and Longevity: Materials research should focus on identifying substances that can retain their structural integrity and performance over extended periods in the harsh space environment, including resistance to wear and degradation.
- Multi-Functional Materials: Advancing the development of materials capable of performing multiple functions—such as providing both thermal protection and radiation shielding—can significantly improve spacecraft design and overall mission efficiency.
Emerging Materials and Technologies
Radiation and Thermal Protection in High-Altitude Aviation: Emerging materials and technologies are revolutionizing protection systems in high-altitude aerospace applications. Notably, graphene-based composites, smart materials, and ultra-lightweight metal foams are at the forefront of this innovation. These advanced materials offer exceptional properties that enhance both performance and safety in demanding aerospace environments.
Graphene-Based Composites
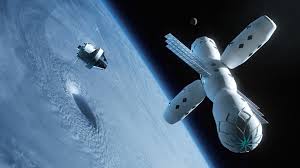
- Exceptional Properties: Graphene materials possess outstanding thermal, electrical, and mechanical properties, making them highly suitable for demanding applications such as aerospace.
- Foam Applications: Reduced graphene oxide (RGO) foams exhibit excellent electromagnetic interference (EMI) shielding and mechanical robustness, making them highly valuable for protecting sensitive aviation electronics.
- Adaptive Properties: To withstand simultaneous thermal and extreme mechanical loading environments, hierarchical composites with self-adaptive anisotropic deformation capabilities are essential for effective thermal protection.
- Biomimetic Design: Materials that incorporate biomimetic structures offer enhanced flexibility and thermal resistance, making them essential for high-performance aerospace applications.
Ultra-Lightweight Metal Foams
- Weight Efficiency: Ultra-lightweight metal foams that maintain structural integrity are essential for high-altitude aviation, where minimizing weight without compromising strength is critical.
- Thermal Barrier Effects: Composite metal foams enhanced with 2D materials like graphene exhibit improved thermal barrier properties, resulting in superior performance under extreme conditions.
These emerging materials are extremely promising, yet innovative materials syntheses are
required due to the high production costs and scaling which limits practical application in
aerospace technologies.
Environmental and Sustainability Considerations
Why Developing Sustainable Materials Is Important
- Environmental Impact: Conventional materials and processes can lead to pollution and resource depletion. Sustainable materials aim to minimize these effects by utilizing eco-friendly production methods and renewable resources.
- Lifecycle Considerations: To support a circular economy, sustainable materials should be designed for ease of recycling, reuse, or environmentally safe disposal at the end of their lifecycle.
- Material Performance: High-altitude applications expose materials to harsh conditions, making it essential for sustainable alternatives to meet stringent performance standards to ensure long-term viability.
- Innovation in Materials: Emerging synthetic fibers and polymers have the potential to create lighter, stronger, and more environmentally friendly materials, addressing both performance and sustainability challenges in aerospace applications.
In-Situ Resource Utilization (ISRU) for Lunar and Martian Materials
- Resource Efficiency: In-Situ Resource Utilization (ISRU) enables the use of local materials on the Moon or Mars, reducing reliance on Earth-based resources and significantly lowering transportation costs.
- Material Production: ISRU enables on-site production by transforming local regolith and other resources into construction materials for habitats, tools, and infrastructure.
- Sustainability: By reducing the need to launch materials from Earth, this approach supports sustainability and minimizes environmental impact—an essential factor in developing advanced thermal protection systems and related technologies for space exploration.
- Long-Term Missions: Sustaining long-duration space missions depends on ISRU to provide essential resources to astronauts on other celestial bodies, reducing the need for constant resupply from Earth.
Advanced manufacturing methods:
Thermal protection and high altitude aviation include novel composites and ceramics designed and tested to optimize performance under extreme conditions. Additive manufacturing and chemical vapor deposition techniques are utilized to generate materials with tailorable material properties to address the demanding high altitude environments.
Radiation Shielding by Additive Manufacturing
- Multi-Material Composites: Advanced radiation shields are being developed using additive manufacturing techniques, such as direct ink writing, to fabricate composites of materials like tungsten and boron nitride. These composites are engineered to attenuate specific types of radiation, thereby enhancing the protective capabilities of space systems.
Thermal Management: In addition to radiation shielding, the anisotropic properties of boron nitride flakes within these composites contribute to improved thermal management. This is crucial for maintaining the functionality of onboard electronics under continuous radiation exposure.
- Ceramic Foams and Composites: Reticulated open-cell ceramic foams and silicon carbide (SiC)-based composites are being evaluated for their mechanical strength and thermal resilience in hypersonic vehicle thermal protection systems
- Testing and Performance: These materials have undergone rigorous testing, including arcjet simulations, and have demonstrated the ability to withstand extreme heat fluxes, confirming their suitability for high-temperature aerospace environments.
- Material Characteristics: Reinforced UHTC materials, such as those combined with carbon or silicon carbide (SiC) fibers, exhibit enhanced high-temperature resistance and superior thermal shock tolerance. These properties make them ideal for demanding aerospace applications, including hypersonic flight and atmospheric re-entry.
Conclusion
Summary of Key Findings
Notable Radiation Protection Materials Development
- Radiation Protection Materials in Aerospace: Recent advancements in aerospace materials have led to the development of radiation shielding capable of withstanding deeply penetrating radiation from solar flares and galactic cosmic rays (GCR). In contrast, historical alternatives lacked the effectiveness needed to defend against the high-energy particles characteristic of GCR, underscoring the importance of modern material innovations for long-duration space missions.
- Recent Advances in Radiation Protection: Current research is increasingly focused on polymeric materials that provide enhanced protection for both humans and electronic equipment aboard spacecraft and high-altitude aircraft. Another critical area of development involves materials capable of attenuating secondary neutrons generated from high-energy particle interactions, further improving overall radiation shielding effectiveness in space environments.
Key Takeaways from Empirical Research and Case Studies:
- Empirical Research Importance: Empirical research is essential to develop condition-specific thermal protection materials tailored for high Mach number and high-altitude environments, ensuring both safety and optimal performance in extreme aerospace conditions.
Case studies show advanced ceramic materials enhance heat and mass transfer characteristics increasingly, hence maintaining acceptable regimes for prolonged flights. Studies reflect the necessity of maintaining the initial geometry of thermal protection materials during flight, which is imperative for aerodynamic efficiency.
Recommendations for Future Research in Material Science:
- Development of Advanced Materials: High-performance advanced ceramic materials for thermal protection in extreme environments require more comprehensive research. Current studies show encouraging results related to flow regimes and structural geometries during flight.
It deals with research into unsteady coupled heat and mass transfers in many materials for the optimization of thermal protection of different flight paths.
- Material Integrity and Operational Performance: Extensive testing is essential to evaluate the durability and functional performance of thermal protection materials under prolonged exposure to extreme high-stress conditions. The findings must be applicable to long-duration missions. Innovations lie in the development of new composite materials that integrate ceramic properties with those of other substances, promising significant advancements in thermal protection efficiency while building upon prior research.
Implications for Future Missions and Industry Applications:
- Enhanced Safety and Functionality: The development of new materials should greatly enhance the safety and operational performance of manned space missions and high-altitude aviation. Additionally, these materials must provide superior heat protection and radiation resistance, which are critical for withstanding extreme environments.
- Cross-Industry Applications of Space Radiation and Thermal Protection Materials: Materials developed for radiation and thermal protection in space environments have the potential to greatly enhance durability and efficiency in high-temperature and high-radiation conditions across various industries, including automotive, energy, and electronics. Moreover, these advancements hold significant promise for aerospace, enabling the creation of more efficient designs and materials that support longer, more ambitious space explorations beyond Earth.
Author Name
Abhina Anil